Engineering & Manufacturing
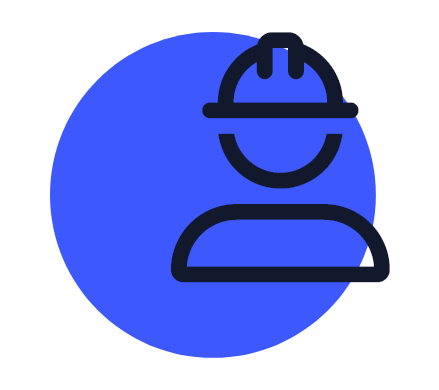
Sector
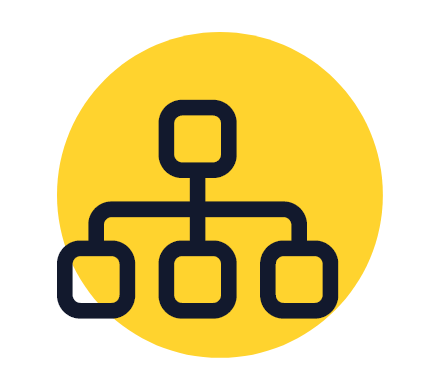
Service
Legacy Software Modernisation
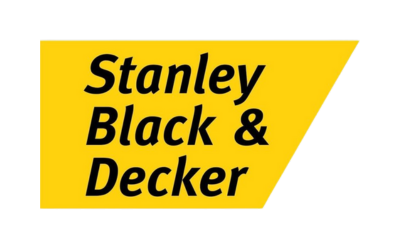
The client
Stanley Black and Decker
Stanley Black & Decker (SBD) is a renowned global provider of hand tools, power tools, and related accessories, serving a diverse range of industries and customers. The company's Technical Services team required a robust solution to manage the engineering Bill of Material (BOM) for products throughout their lifecycle, from launch through revisions to 'end of life'. The first phase of the project streamlined global processes, removed silos, and delivered automation. This gave the Technical Services team control of warehouse inventory and supply chain, reducing wastage and improving time to market. The next phase involved PDMS supporting SBD's Service and Repair Agents around the world to streamline and manage their data.
The challenge
Current interfacing issues
SBD faced several challenges with their existing systems. They had two separate applications that provided infrequent updates to websites used by Service and Repair Agents for technical information and sourcing parts. Additionally, these applications were used to manually extract and supply data to their SAP Enterprise Resource Planning (ERP) software, which was time-consuming and error prone.
The solution
Improved accuracy and performance
PDMS collaborated with the SBD team to develop an interfacing solution for the new BOM system to integrate with two existing websites used by Service and Repair Agents for technical information and part sourcing. Additionally, the solution provided automation for the previously manual and error-prone process of transferring data between the BOM system and the SAP ERP.
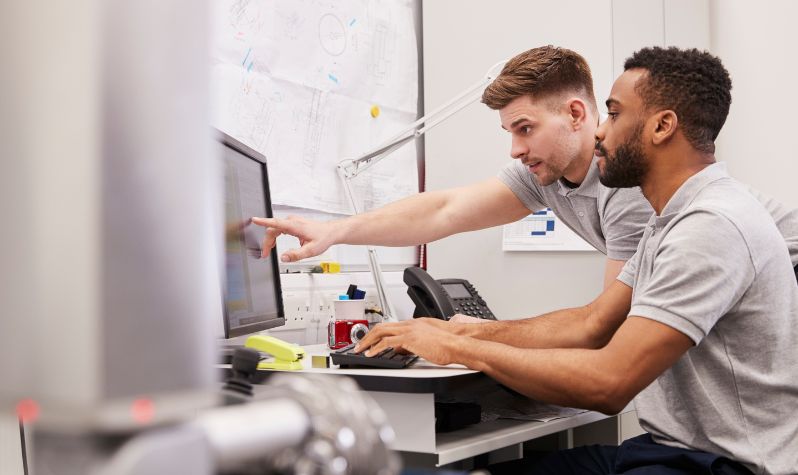
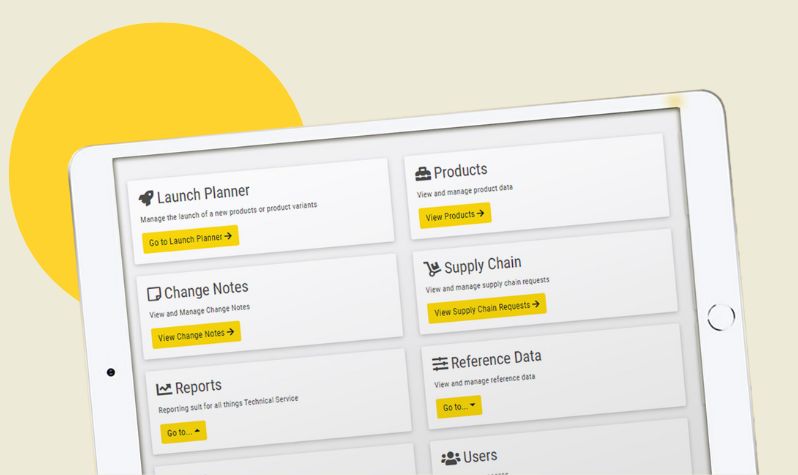
The project
The second phase of the project focused on resolving interfacing issues. PDMS developed an API-based solution to send product data in JSON format to Microsoft middleware, improving data accuracy and frequency on the existing websites. This allowed the websites to reflect the latest product and part updates, serving images and exploded diagrams directly from the PDMS cloud infrastructure for enhanced global performance.
A subsystem was also created within the BOM system to manage job scheduling, error handling, and reporting. This gave the Technical Services team full control over the data published on the websites.
For SAP ERP integration, PDMS developed API endpoints to automate inventory creation, depletion, and pricing updates. This ensured the SAP system remained in sync with the BOM system, benefiting departments like supply chain and improving decision-making based on real-time data.
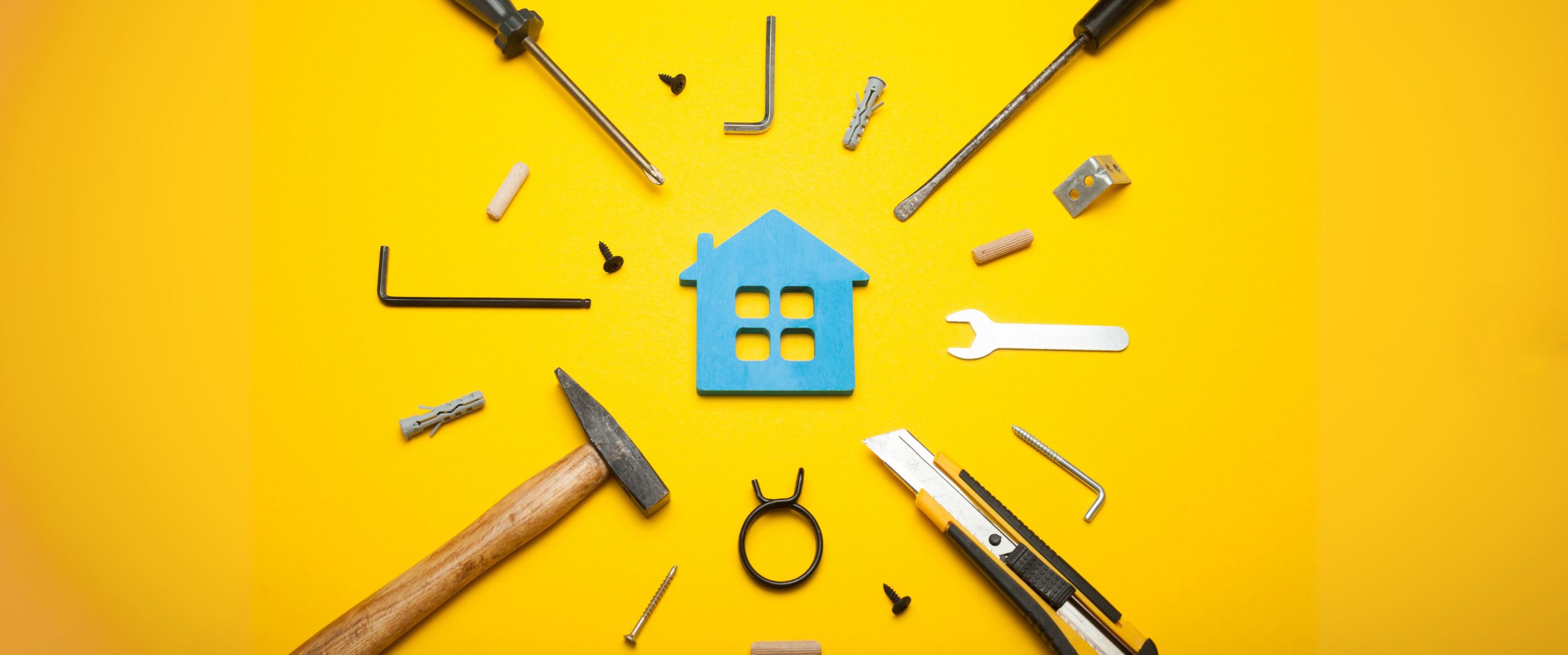
The results
The new BOM system now supports the automatic creation and depletion of part inventory in SAP, ensuring coordinated financial processes. It also enables the automatic update of part and warehouse status, providing the supply chain and other associated departments with the latest information for informed decision making. Additionally, the update of inventory pricing allows the Technical Services teams to develop products cost-effectively and profitably.
A subsystem was also developed within the new BOM system to handle job scheduling, error reporting and handling. The Technical Services team are now in full control of the data published via the websites.
The benefits
The implementation of the new BOM system has bridged many gaps between departments and regions globally, transforming SBD’s Technical Services capability. The automation of data transfer processes has enhanced accuracy and efficiency, reducing manual errors and saving time. The improved data accuracy and high-frequency updates on the websites have significantly enhanced the user experience for Service and Repair Agents. Ultimately, the new system has provided Stanley Black & Decker with a modern, scalable solution that supports their business needs and drives operational efficiency.
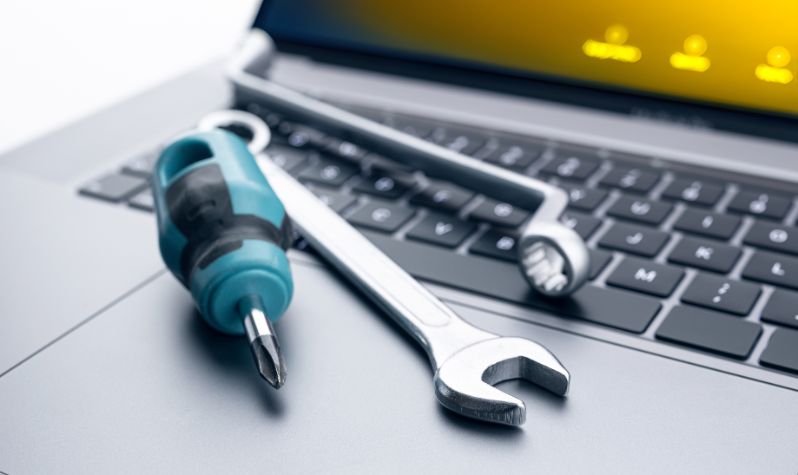
More case studies
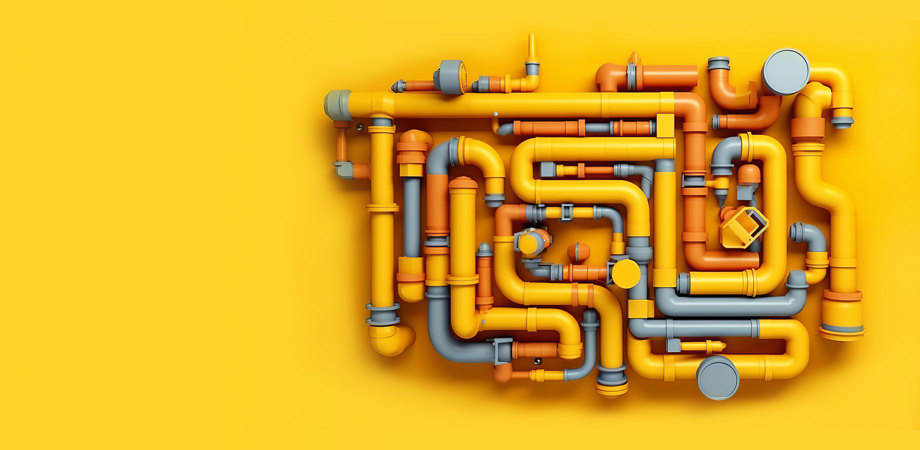
Unlocking the hidden value in a legacy ERP system
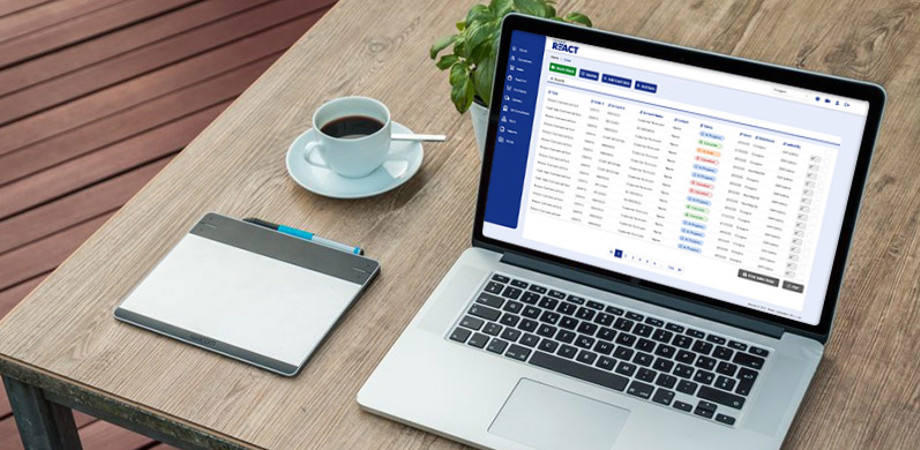
Modernising legacy ERP system and improving UX
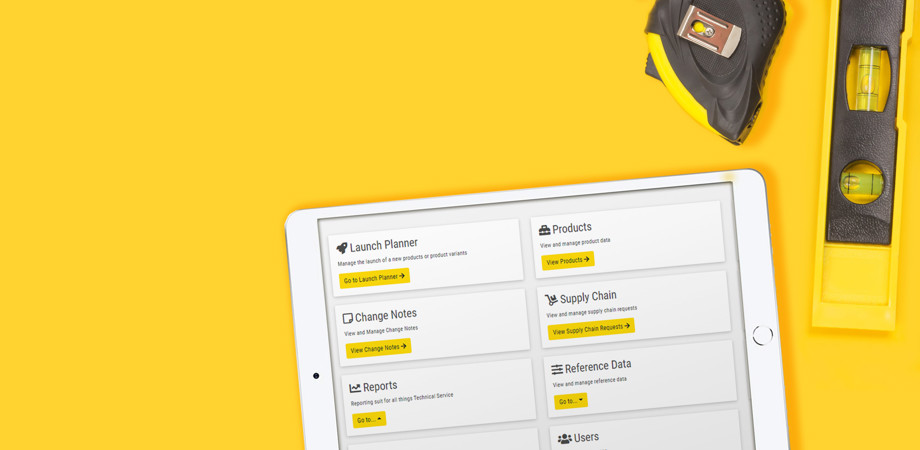